Table of Contents
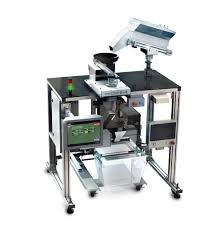
In the world of small parts manufacturing, precision and efficiency are everything. Whether you’re in the electronics, medical, automotive, or hardware industry, counting and packaging tiny components can be a tedious and error-prone task if done manually. This is why investing in the best counting machine for small parts manufacturing is essential for improving productivity, accuracy, and overall operational efficiency.
But with so many different models and technologies available, how do you choose the right one? This article explores the importance of automated counting, key features to look for, different types of machines, and how to choose the best one for your specific manufacturing needs.
Why Small Parts Manufacturers Need a Counting Machine
In small parts manufacturing, accuracy and efficiency are essential to maintaining productivity and profitability. Whether a company produces electronics, medical components, automotive fasteners, or hardware, the task of accurately counting and sorting small parts can become an operational bottleneck if done manually. Even the most experienced workers can make errors when handling thousands of tiny components daily, leading to inventory discrepancies, order fulfillment mistakes, and wasted resources.
To solve this challenge, businesses are turning to automated counting machines—specialized devices designed to quickly and accurately count small parts with minimal human intervention. These machines not only improve accuracy but also streamline production, reduce waste, and ensure regulatory compliance. Below, we explore the key reasons why every small parts manufacturer should consider investing in an automated counting solution.
1. Eliminating Human Error
One of the biggest risks in manual counting is human error. Whether counting screws, bolts, washers, circuit board components, or plastic fittings, the repetitive nature of the task makes it prone to miscounts and inconsistencies. Workers may:
- Lose track of the count due to distractions or fatigue
- Overcount or undercount due to small size or uniform appearance of parts
- Accidentally mix different components, leading to quality control issues
- Struggle with batch counting, especially when dealing with thousands of items per order
Errors in manual counting can result in incorrect inventory records, delays in order fulfillment, and customer dissatisfaction. In industries where precision is critical—such as medical device manufacturing or aerospace components—a small miscalculation could lead to compliance issues or even safety risks.
How Automated Counting Machines Eliminate Errors
Automated counting machines remove the guesswork and inconsistency of manual counting by using advanced technologies such as:
- Optical sensors to visually scan and count individual parts
- Vibratory bowl feeders that align and count parts mechanically
- Weight-based counting systems that determine the exact number of pieces based on total weight
- Laser or infrared detection for high-speed part recognition
With accuracy rates above 99%, these machines ensure that each batch is counted precisely, eliminating costly errors and improving overall workflow efficiency.
2. Increasing Efficiency and Productivity
For manufacturers dealing with high-volume orders, manually counting thousands of tiny parts is not only inefficient but also a waste of valuable labor resources. Workers must dedicate significant time and effort to the task, often requiring multiple employees to double-check counts and verify accuracy. This slows down production and increases labor costs without adding real value to the business.
How Counting Machines Boost Productivity
An automated counting machine can handle in minutes what would take hours manually. Depending on the model, some machines can process thousands of parts per minute, allowing workers to focus on higher-value tasks such as quality control, machine operation, or assembly work.
Benefits of automation in small parts manufacturing:
- Faster order fulfillment – Automating the counting process reduces lead times and improves customer satisfaction
- Less downtime – Workers no longer need to stop production to manually verify quantities
- Scalability – As demand grows, counting machines can easily handle increased production volume
- Reduced labor costs – Businesses can reallocate employees to more critical tasks instead of manual counting
Companies that integrate automated counting technology can streamline production, improve throughput, and remain competitive in fast-moving industries.
3. Reducing Material Waste
Accurate counting is not just about meeting production quotas—it also directly impacts cost efficiency. When parts are miscounted, businesses risk overpacking or underpacking orders, leading to:
- Excess material waste – Overcounting means giving away extra components that cut into profit margins
- Customer complaints – Undercounting results in incorrect shipments that lead to refund requests or contract disputes
- Inventory discrepancies – Inaccurate counts can disrupt supply chain planning and stock replenishment
How Counting Machines Help Reduce Waste
A high-precision counting machine ensures that each package contains the exact number of components needed, preventing unnecessary waste and improving cost efficiency. Manufacturers benefit from:
- More accurate inventory tracking, ensuring stock levels match real-world demand
- Better cost control, reducing product giveaway and unnecessary reorders
- Higher customer satisfaction, as buyers receive their orders correctly and on time
For industries where precision packaging is essential—such as electronics, pharmaceuticals, and aerospace—automated counting technology is a critical investment for minimizing waste and maximizing profit margins.
4. Meeting Industry Standards and Compliance Requirements
Certain industries require strict regulatory compliance when it comes to inventory control, batch tracking, and order fulfillment. For example:
- Medical device manufacturers must comply with FDA regulations to ensure accuracy in production
- Aerospace and defense contractors must adhere to ISO and AS9100 standards
- Pharmaceutical companies must meet stringent packaging guidelines to ensure product safety
Failing to comply with industry standards can result in:
- Legal consequences, including fines or contract penalties
- Loss of business, as customers demand higher precision and traceability
- Damaged reputation, making it harder to secure future contracts
How Automated Counting Ensures Compliance
Automated counting machines can integrate with ERP and quality management systems, ensuring every batch is:
- Tracked and recorded for auditing purposes
- Packaged with consistent accuracy, reducing the risk of compliance failures
- Labeled correctly with precise quantity information
For manufacturers operating in highly regulated industries, investing in automated counting solutions helps maintain consistency, accuracy, and legal compliance while improving operational efficiency.
Key Features to Look for in a Small Parts Counting Machine
Not all counting machines are created equal. When searching for the best counting machine for small parts manufacturing, consider the following features:
1. Counting Technology
Different machines use different technologies to count small parts accurately. Some of the most common include:
- Optical Scanning: Uses cameras and sensors to visually count objects in real time. Ideal for lightweight or irregularly shaped parts.
- Vibratory Bowl Feeders: Uses vibration to align and count parts as they move along a conveyor. Best for metal hardware or small plastic parts.
- Weight-Based Counting: Measures the total weight of a batch and divides it by the weight of a single item. Effective for uniform parts like pills, beads, or fasteners.
- Laser or Infrared Sensors: Detects and counts components as they pass through a laser beam. Great for high-speed manufacturing lines.
2. Speed and Throughput
How many parts do you need to count per minute? Some machines are designed for high-speed production lines, while others are better for smaller-scale operations. Look for machines that can meet your demand without compromising accuracy.
3. Accuracy and Tolerance Levels
Even a small miscalculation in a batch can cause significant issues. Choose a machine that offers high accuracy (99% or greater) and low error margins, especially if dealing with critical components.
4. Compatibility with Part Sizes and Shapes
Some machines are designed specifically for uniform, small, round components, while others can handle irregular shapes, flexible materials, or lightweight parts. Ensure the machine is compatible with the range of products you manufacture.
5. Integration with Existing Systems
Modern counting machines often feature digital interfaces, automated sorting, and data logging capabilities. If you use an ERP (Enterprise Resource Planning) system or an inventory management platform, look for a machine that can seamlessly integrate with your existing technology.
6. Durability and Maintenance
Industrial counting machines can experience heavy use, so durability is key. Look for models made from stainless steel or industrial-grade materials that can withstand continuous operation. Additionally, ease of maintenance—such as self-cleaning mechanisms or accessible parts—will save time and reduce downtime.
Types of Counting Machines for Small Parts Manufacturing
Depending on your specific needs, there are several types of counting machines to consider:
1. Vibratory Bowl Feeders
Best for: Metal fasteners, plastic parts, screws, washers, and electronic components
How it works: Uses vibration to align and count parts as they move through a sorting system.
2. Optical Counting Machines
Best for: Delicate or irregularly shaped items such as medical components or semiconductor parts
How it works: Uses advanced camera technology and image recognition software to detect and count individual components.
3. Weighing Scales with Counting Functionality
Best for: Pills, beads, uniform plastic pieces, and small identical parts
How it works: Measures the total weight of a batch and divides it by the known weight of a single item.
4. Conveyor-Based Counting Machines
Best for: High-speed manufacturing lines requiring bulk counting
How it works: Uses infrared sensors or lasers to detect and count parts as they move along a conveyor belt.
Choosing the Best Counting Machine for Your Business
When selecting a counting machine, consider the following:
- Production Volume: If you need to count thousands of parts per minute, opt for high-speed models like vibratory feeders or conveyor-based machines.
- Precision Requirements: For delicate or high-value components, optical counting or laser-based systems offer superior accuracy.
- Budget: Basic weight-based counters are more affordable, while AI-driven optical scanners tend to be pricier but offer advanced capabilities.
- Scalability: If your business plans to grow, invest in a machine that can handle increased production demand.
For small parts manufacturers, investing in an accurate counting solution is essential for reducing errors, improving efficiency, and maintaining compliance with industry standards. While an automated counting machine can be a game-changer, not all businesses have the capacity or need to purchase their own equipment.
If your company requires precise electronic counting services rather than owning a machine, Miniature Folding Inc. offers advanced electronic counting solutions tailored to industries such as pharmaceuticals, nutraceuticals, and cosmetics. Their expertise in precision packaging ensures that your products are counted, packed, and delivered with the highest level of accuracy and quality control.
Additionally, if your business needs high-quality printing and folding services for packaging inserts, Miniature Folding can provide customized solutions to meet your specific requirements. Instead of investing in costly equipment, partnering with a specialized service provider like Miniature Folding allows manufacturers to streamline operations while ensuring top-tier precision and compliance.
